9 Simple Techniques For Die Castings
Wiki Article
The Only Guide for Manufacturing
Table of ContentsFacts About Additive Manufacturing UncoveredA Biased View of Manufacturing IndustriesThe Ultimate Guide To Manufacturing IndustriesUnknown Facts About Die Casting
With injection moulding, pre-dried granular plastic is fed by a forced ram from a hopper right into a warmed barrel. As the granules are slowly moved ahead by a screw-type bettor, the plastic is pushed into a warmed chamber, where it is thawed. As the bettor advances, the thawed plastic is compelled via a nozzle that relaxes versus the mould, allowing it to enter the mould cavity with an entrance and also runner system.The sequence of events throughout the shot mould of a plastic part is called the shot moulding cycle. The cycle starts when the mould closes, followed by the shot of the polymer right into the mould cavity. As soon as the dental caries is filled up, a holding stress is kept to make up for material shrinking.

When the dental caries is 98% complete, the equipment switches from speed control to stress control, where the tooth cavity is "loaded out" at a constant stress, where enough speed to get to wanted stress is required. This lets workers manage part dimensions to within thousandths of an inch or far better. Various kinds of injection moulding processes [edit] A lot of injection moulding procedures are covered by the conventional process summary above, there are several essential moulding variations including, yet not restricted to: An even more detailed checklist of shot moulding procedures might be found right here: Process troubleshooting [ modify] Like all commercial procedures, shot molding can create problematic components, even in toys.
The 4-Minute Rule for Manufacturing
Tests are commonly executed prior to full production runs in an effort to anticipate defects as well as establish the appropriate specifications to make use of in the shot process.: 180 When filling a new or unfamiliar mould for the initial time, where shot dimension for that mould is unidentified, a technician/tool setter might perform a trial run before a full production run.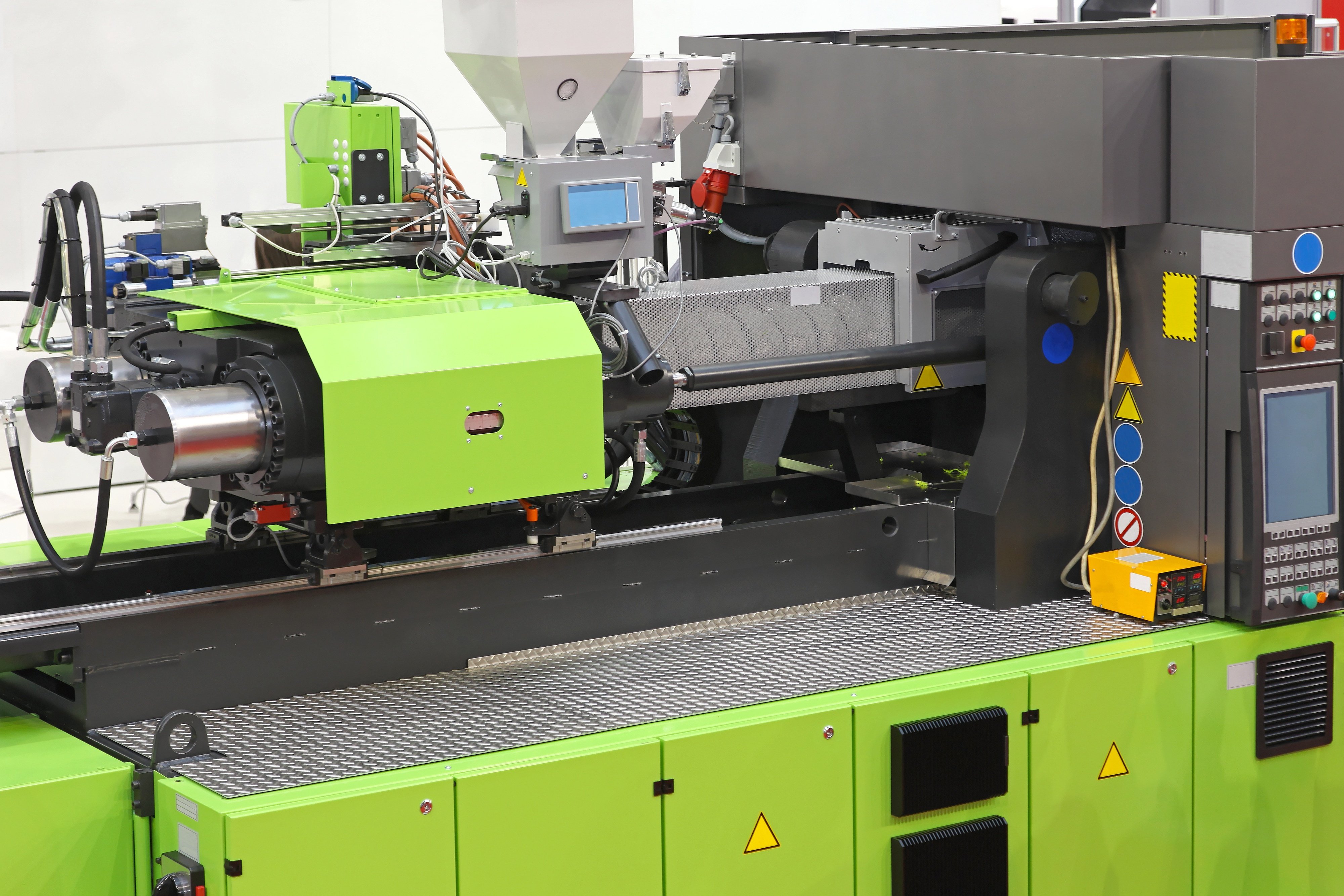
Holding pressure is enhanced until the parts are devoid of sinks as well as part weight has actually been achieved. Molding issues [modify] Shot moulding is an intricate modern technology with possible manufacturing problems. They can be created either by defects in the moulds, or more frequently by the moulding process itself.: 4785 Moulding issues Alternate name Descriptions Causes Sore Blistering Increased or layered area on surface area of the part Device or material is too hot, usually triggered by a lack of cooling down around the tool or a faulty heating system.
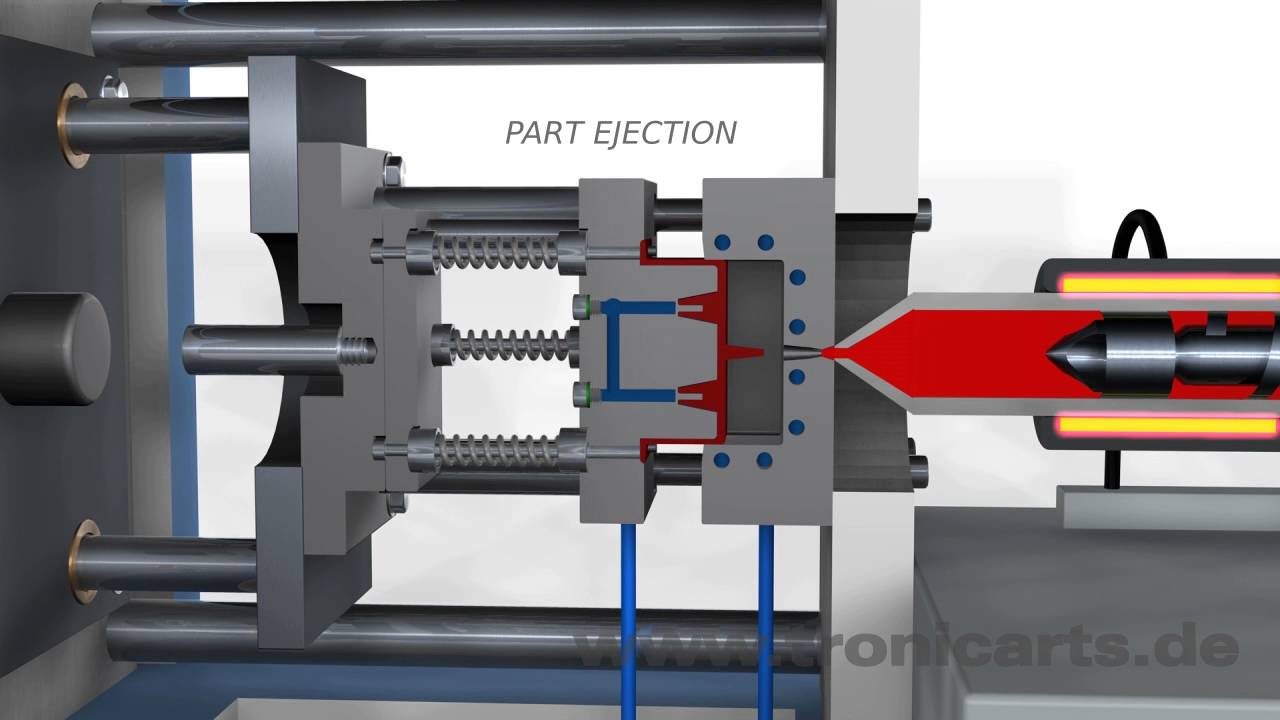
The Greatest Guide To Manufacturing Industries
Embedded particulates International bit (burned product or various other) embedded in the component Particles on the tool surface area, polluted product or international debris in the barrel, or also much shear heat melting the product prior to shot. Circulation lines Directionally "off tone" wavy lines or patterns Shot speeds as well slow (the plastic has cooled down excessive throughout shot, injection rates need to be set as rapid as is suitable for the procedure and material made use of).Loading as well quickly, not allowing the sides of the part to establish. Also mould may run out registration (when the 2 fifty percents don't centre correctly and also part walls are not the very same thickness). The supplied details is the common understanding, Adjustment: The Absence of pack (not holding) stress (pack stress is used to pack out although is the component throughout the holding time).
To put it simply, as the component shrinks the resin separated from itself as there was not adequate resin in the dental navigate to this site caries. The gap could happen at any type of location or the component is not restricted by the density but by the resin circulation and design for manufacturing also thermal conductivity, yet it is most likely to happen at thicker areas like ribs or bosses.
Knit line/ Meld line/ Transfer line Discoloured line where two flow fronts satisfy Mould or worldly temperatures set too low (the product is cool when they satisfy, so they don't bond). Time for shift between shot and transfer (to packaging and also holding) is prematurely. Twisting Altered part Air conditioning is also short, product is as well warm, absence of cooling down around the device, wrong water temperature levels (the components bow inwards towards the hot side of the tool) Unequal diminishing in between areas of the component.
The Facts About Mfg Revealed
125 inch wall thickness is +/- 0. 008 inch (0. 2 mm).: 446 Power requirements [modify] The power needed for this procedure of injection moulding relies on several points and varies in between materials utilized. Manufacturing Processes Reference Overview states that the power demands depend on "a product's details gravity, melting factor, thermal conductivity, part size, and molding price." Below is a table from web page 243 of the very same reference as formerly discussed that best highlights the features pertinent to the power required for the most frequently utilized products.In addition to mounting examination systems on automated gadgets, multiple-axis robots can remove parts from the mould as well as place them for additional procedures. Particular instances include removing of parts from the mould right away after the components are developed, in addition to using equipment vision systems. A robotic grips the part after the ejector pins have been reached free the part from the mould.
Why is web injection molding equipment production so efficient? And exactly how does it function? To discover, allow's dig into the subject and address every one of the important concerns, including what it is, the process behind it, its primary benefits, and also exactly how to pick the best company. What is Shot Molding? is the process of making use of plastic to make a wide variety of components as well as items.
The shot molding device uses customized mold and mildews to fill them out according to specifications, developing similar copies that can be personalized in a selection of ways. What's even more, injection molding is a really versatile process, permitting a vast array of various products and finishes, that makes it a preferred alternative in plenty of industries with totally various goals and demands - mfg.
Report this wiki page